Aluminum vs Copper Crush Washer- A Comparative Analysis
When it comes to sealing connections in various mechanical and automotive applications, crush washers play a critical role in preventing leaks and ensuring a tight fit. These small but crucial components are often overlooked, yet their choice can significantly impact the overall performance and reliability of the system they are employed in.
Among the most commonly used materials for crush washers are aluminum and copper, each offering distinct advantages and disadvantages. In this discussion, we will explore the differences between copper vs aluminum crush washers, their properties, and the situations in which one material might be preferred over the other.
What is a Crush Washer?
A crush washer, also known as a compression washer, is a type of sealing washer designed to provide a tight and leak-free seal between two interlocking surfaces. The primary purpose of a crush washer is to prevent fluid or gas leakage at the joint by deforming under pressure, creating a reliable seal.
Crush washers are designed to be deformed under pressure, creating a secure seal between two interconnected surfaces. The construction of a crush washer typically involves a soft and malleable material that can easily conform to the irregularities and imperfections of the mating surfaces. This ensures that the washer creates a uniform seal, even in cases where the surfaces may not be perfectly flat or smooth.
When a crush washer is tightened between the two surfaces, the pressure causes the washer to deform and fill any gaps or irregularities, effectively sealing the connection. As the name suggests, the washer is ‘crushed’ or compressed during the tightening process, hence the term ‘crush washer.’
Crush washers are widely used in automotive engines and transmissions, hydraulic systems, plumbing connections, aerospace components, and many other areas where a reliable and leak-proof seal is essential. They come in various sizes and thicknesses to accommodate different thread sizes and pressure requirements.
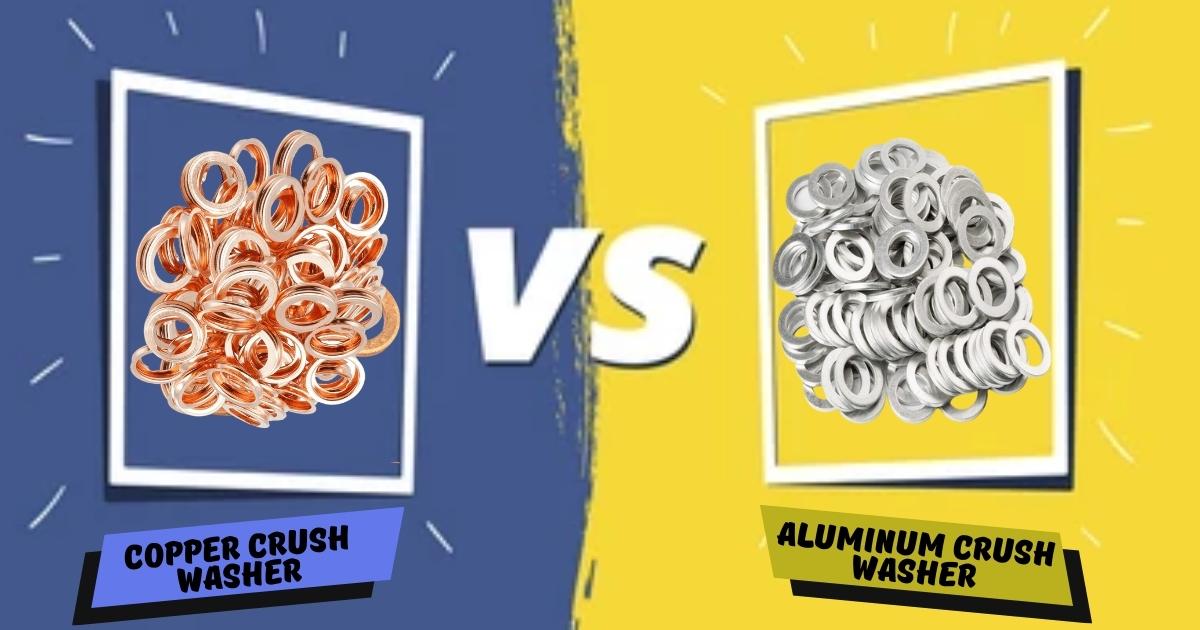
Aluminum vs Copper Crush Washer
As we have already stated, the most common materials used for crush washers are aluminum and copper, each offering its own set of advantages and characteristics. Aluminum crush washers are lightweight and have good corrosion resistance, making them suitable for a wide range of applications.
On the other hand, copper crush washers are known for their excellent thermal conductivity and are often used in high-temperature applications. Let’s dive into the details!
Aluminum Crush Washer
An aluminum crush washer is a type of sealing washer made from aluminum, which is designed to create a reliable seal between two joining surfaces. These washers are commonly used in various industries and applications where threaded connections are involved, such as automotive, plumbing, hydraulic systems, and more.
Key Characteristics and Features of Aluminum Crusher Washers
Lightweight
Aluminum is a lightweight metal, making the crush washers suitable for applications where weight is a critical factor, especially in industries like aerospace and automotive. The lightweight nature of aluminum crush washers also simplifies handling and installation processes, particularly in large-scale industrial applications. This ease of handling makes it more convenient for workers during assembly or maintenance tasks as it reduces the strain and effort required.
Corrosion Resistance
Aluminum naturally forms a thin oxide layer on its surface, which provides inherent corrosion resistance. This oxide layer acts as a protective barrier, preventing further corrosion and degradation of the metal. As a result, aluminum crush washers are well-suited for applications that are exposed to moisture or certain chemicals.
In environments where moisture is present the oxide layer ensures they can maintain a reliable seal over time. Ideally, the washers can withstand exposure to water, engine oil, transmission fluid, and other fluids without deteriorating or causing leaks.
Malleability
The malleability of aluminum is a key advantage for aluminum crush washers. Being relatively soft and easily deformable, aluminum washers can adapt to the irregularities and imperfections of interlocking surfaces when subjected to pressure during tightening.
This characteristic ensures that the crush washer can create a tight and uniform seal, even if the surfaces are not perfectly flat or smooth. The ability of the aluminum crush washer to conform to the mating surfaces helps to fill any gaps or irregularities, ensuring a secure and leak-free connection.
Thermal Conductivity
While aluminum is not as thermally conductive as copper, it still possesses moderate thermal conductivity. This can be advantageous in certain applications where some heat dissipation is required. For instance, in applications where there is a need to transfer heat away from a component or system, the aluminum crush washer can play a role in assisting with heat dissipation.
Ideally, as heat is generated during operation, the crush washer can help conduct and distribute the heat away from the connection point, thereby preventing overheating and maintaining optimal operating temperatures.
Drawbacks
Lower temperature limit- Aluminum crush washers may not be suitable for extremely high-temperature applications due to their lower melting point.
Lower strength- Aluminum-based crush washers might not be the best choice for applications requiring high load-bearing capacity or resistance to heavy mechanical stresses.
Reduced wear resistance- Aluminum crush washers tend to wear out more quickly in abrasive conditions or repetitive movements.
Compatibility issues- Aluminum crush washers may also not be compatible with certain fluids or chemicals. As such you may want to consider material compatibility carefully before using aluminum-based crush washers.
Copper Crush Washer
A copper crush washer is a specialized type of sealing washer crafted from copper. Its widespread application in automotive, plumbing, and mechanical fields stems from its remarkable ability to establish a dependable seal between two surfaces. Copper-based crush washers are commonly used in automotive engines, exhaust systems, and industrial machinery, where efficient heat dissipation and reliable sealing are critical.
Key Characteristics and Features Copper Crush Washers
Excellent Thermal Conductivity
Generally, copper is a highly efficient thermal conductor. This makes copper washers ideal for applications where heat dissipation is crucial. The washers can effectively transfer heat away from the connection, which helps prevent overheating in components and systems.
In situations where overheating can be detrimental to the performance and reliability of equipment, copper crush washers play a critical role in maintaining optimal operating temperatures. They achieve this by preventing thermal stress, which can lead to component failure or reduced lifespan.
Good Electrical Conductivity
Copper is renowned for being an excellent conductor of electricity, meaning it allows electric currents to flow through it efficiently. This property makes it particularly well-suited for electrical applications where the continuity and efficiency of electrical flow are essential.
Copper crush washers find valuable applications in electrical connections for various industries, including automotive, electronics, and power distribution. You can utilize them in electrical panels, grounding systems, battery terminals, and other critical connections where maintaining reliable electrical conductivity is paramount.
Strength
Copper crush washers are highly regarded for their exceptional strength and hardness, making them reliable for sealing components under extreme pressure. The strength of copper crush washers enables them to withstand significant compressive forces without deforming or failing, ensuring a secure and tight seal between the surfaces.
When subjected to high pressure during tightening, copper crush washers maintain their structural integrity by distributing the force evenly across the sealing surface. This characteristic prevents leaks and ensures a dependable seal, even in demanding environments where pressure fluctuations are common.
Corrosion Resistance
Copper crush washers offer inherent corrosion resistance, although it may not be as robust as aluminum in certain environments. Nonetheless, this natural resistance makes them well-suited for diverse applications where exposure to moisture or specific chemicals is a concern.
This valuable attribute makes copper crush washers excel in outdoor and marine environments, where they withstand the effects of moisture and salt water. Additionally, in industries such as construction and architecture, copper crush washers find use in applications regularly exposed to outdoor elements or humid conditions, since they can maintain their sealing effectiveness over time.
Drawbacks
Higher cost- Copper crush washers are generally more expensive than materials like aluminum.
Susceptible to corrosion- While copper possesses natural corrosion resistance, it may not be as effective as materials like aluminum in highly corrosive environments.
Softness and deformation- Copper crush washers can be relatively soft and prone to deformation under high pressure.
Differences Between Aluminum and Copper Crush Washers
One significant difference between aluminum crush washers and their Copper counterparts lies in their material properties. Aluminum crush washers are lightweight, making them ideal for weight-sensitive applications. In addition, they possess moderate thermal conductivity and corrosion resistance due to the thin oxide layer formed on their surface.
On the other hand, Copper crush washers are known for their excellent electrical conductivity and natural corrosion resistance. Being ductile and malleable, they easily conform to interlocking surfaces, ensuring a tight and reliable seal.
While both materials can create reliable seals, copper’s superior strength and hardness provide an added advantage, especially in high-pressure applications. Copper crush washers have the ability to withstand significant compressive forces without deforming or failing, ensuring a secure and tight seal between surfaces.
Application-specific considerations are equally important in the selection process. Assessing compatibility with different fluids and temperatures, as well as the impact of pressure and vibration, will help determine the ideal material for a particular application. Each material’s unique properties can influence its performance in specific environments, so understanding these factors is essential.
Additionally, cost and availability are vital factors to consider when choosing between aluminum and copper crush washers. Aluminum crush washers are often more cost-effective and readily available compared to copper washers. On the other hand, the initial higher cost of copper crush washers may impact budget considerations, making aluminum a more accessible option for certain applications.
Comparing the properties of both materials, aluminum has the advantage of being lightweight, making it suitable for weight-sensitive applications. It also offers corrosion resistance and non-magnetic properties, making it useful in various industries. On the other hand, copper exhibits exceptional strength and boasts excellent thermal and electrical conductivity, making it a preferred choice for specialized applications.
You may also Read: Why is My Key Fob So Sensitive? Causes and Fixes
Generally, the choice between aluminum and copper crush washers depends on the specific requirements of the application. Each material has unique advantages and drawbacks, and understanding their properties and characteristics will help determine the most suitable option for achieving reliable and efficient sealing solutions.
The Parting Shot
When selecting the ideal crush washer material, it is crucial to align it with the specific requirements and considerations of the application. Factors such as pressure, temperature, compatibility with fluids, mechanical stresses, and budget constraints should be carefully evaluated to make an informed decision. Overall, aluminum’s lightweight and corrosion-resistant properties make it a cost-effective choice, while copper offers strength, hardness, and excellent conductivity but at a higher cost.